
What is replacing lithium-ion batteries?
Emerging alternatives to lithium-ion batteries include sodium-ion, potassium-ion, zinc-based systems, flow batteries, and thermal storage technologies. Sodium-ion offers cost-effective scalability using abundant materials, while potassium-ion combines high energy density (160–180 Wh/kg) with streamlined manufacturing. Flow batteries excel in grid-scale longevity (20,000+ cycles), and thermal storage leverages heat retention for renewable energy buffering. Pro Tip: Evaluate applications holistically—high-power needs favor supercapacitors, whereas multi-hour storage suits flow batteries.
How to Safely Dispose of and Recycle Car Batteries
Why is sodium-ion gaining traction as a lithium alternative?
Sodium-ion batteries utilize earth-abundant sodium instead of scarce lithium, cutting material costs by 30–40%. Their low-temperature resilience (-20°C operation) and 4,000-cycle lifespan make them viable for stationary storage and short-range EVs.
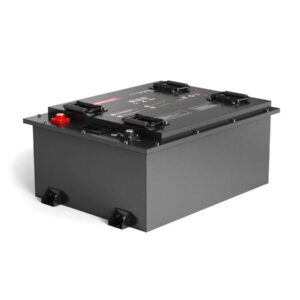
Beyond cost advantages, sodium-ion chemistry avoids lithium’s geopolitical constraints—China controls 80% of lithium refining versus sodium’s global availability. Technical hurdles remain: energy density peaks at 160 Wh/kg (vs. lithium’s 250+ Wh/kg), limiting electric vehicle range. However, recent cathode innovations using layered oxides have boosted capacity retention to 92% after 1,000 cycles. For example, CATL’s first-gen sodium-ion packs power two-wheelers for 150 km per charge. Pro Tip: Pair sodium-ion with lithium hybrids to balance energy density and cost in modular battery systems.
Why consider sodium when performance trails lithium? The answer lies in total system economics—sodium’s raw material costs $150/ton versus lithium carbonate’s volatile $15,000–$70,000/ton pricing.
What breakthroughs define potassium-ion battery development?
Potassium-ion technology achieves lithium-like energy density (180 Wh/kg) using commercial graphite anodes, enabling drop-in replacement potential. Group1’s 18650 cells demonstrate 3.7V operation with 95% capacity retention after 800 cycles.
The secret lies in potassium’s ionic mobility—its +1 charge and 3.6Å radius enable faster intercalation than sodium. This translates to superior rate capability (5C continuous discharge) for power tools and EV acceleration phases. However, dendrite formation at the anode remains a challenge. Researchers at Stanford mitigate this through self-healing polymer coatings that redistribute potassium ions evenly. Real-world testing shows prototype e-bike batteries delivering 80 km range in -10°C conditions. Pro Tip: Use pulse charging protocols to prevent potassium plating during fast-charge cycles. While not yet mainstream, potassium-ion’s compatibility with existing Li-ion infrastructure (same casing, BMS) gives it a commercialization edge over more exotic alternatives.
Parameter | Potassium-Ion | Lithium-Ion |
---|---|---|
Energy Density | 160–180 Wh/kg | 200–300 Wh/kg |
Cycle Life | 800–1,200 | 1,000–2,000 |
Raw Material Cost | $80/ton (K₂CO₃) | $15k–$70k/ton (Li₂CO₃) |
How do flow batteries address long-duration storage needs?
Vanadium redox flow batteries (VRFBs) provide unmatched cycle longevity (20,000+ cycles) through liquid electrolyte regeneration. Their decoupled power/energy scaling allows custom duration (4–100+ hours) by increasing tank size.
Unlike solid-state batteries, VRFBs store energy in vanadium ions dissolved in sulfuric acid—pumped through membrane stacks during charge/discharge. This design eliminates capacity fade from electrode degradation. A 100 MW/400 MWh installation in Dalian, China, demonstrates 80% round-trip efficiency over 20 years. But vanadium’s $25/kg price drives innovation in iron-chromium and organic flow variants. For instance, Form Energy’s iron-air battery achieves $20/kWh capital cost using rusting-reversal chemistry. Pro Tip: Deploy flow batteries where footprint isn’t constrained—their 30 Wh/L energy density requires 5× more space than Li-ion equivalents. Why accept bulky systems? Because they outlast lithium alternatives 10:1 in cycle life for solar farms.
Can supercapacitors complement battery storage effectively?
Supercapacitors deliver instantaneous power bursts (10–100 kW/kg) and million-cycle endurance, bridging gaps where batteries lag. Hybrid systems pair them with Li-ion for regenerative braking energy capture in EVs.
Using activated carbon electrodes and ionic liquid electrolytes, supercaps achieve 95% efficiency in 2-second charge/discharge cycles. Their weakness? Energy density caps at 10 Wh/kg—enough for subway acceleration but insufficient for sustained loads. Tokyo’s Yamanote Line trains use 3.3V/3,000F modules to recover braking energy, reducing grid draw by 30%. Pro Tip: Size supercaps to handle peak loads, letting batteries handle baseline demand. Material advances like graphene-enhanced electrodes promise 60 Wh/kg densities within 5 years—potentially enabling standalone use in short-route delivery vehicles.
Metric | Supercapacitors | Li-ion Batteries |
---|---|---|
Power Density | 10–100 kW/kg | 1–3 kW/kg |
Cycle Life | 1,000,000+ | 1,000–2,000 |
Cost per kWh | $10,000 (energy) | $100–$300 |
What role does thermal storage play in energy systems?
Molten salt and phase-change materials store heat at $15–25/kWh, undercutting Li-ion’s $100+ costs for multi-day storage. Rondo Energy’s brick-based systems reach 1,500°C with 95% daily efficiency.
Thermal storage shines in industrial applications—a German cement plant uses 1,200°C ceramic beds to buffer waste heat, cutting natural gas use by 40%. Electricity-to-heat conversion via resistance or heat pumps achieves 70–90% efficiency, with steam turbines converting back at 50–60%. While round-trip efficiency trails batteries (35–50% vs 80–95%), 100-hour discharge capability makes it indispensable for renewable-heavy grids. Pro Tip: Combine thermal storage with combined-cycle plants—excess wind power can preheat feedwater, boosting overall efficiency to 65%.
Battery Expert Insight
FAQs
Are any lithium alternatives commercially viable today?
Sodium-ion enters mass production in 2025 for two-wheelers and backup power, while flow batteries dominate 4+ hour grid projects. Potassium-ion remains in pilot phases but shows strong EV potential.
Which technology threatens Li-ion dominance first?
Sodium-ion will capture 15% of the stationary storage market by 2030 due to raw material economics. Its LFP-like safety profile accelerates adoption in residential ESS.
Do alternatives compromise on energy density?
Most do—except potassium-ion matching LFP’s 180 Wh/kg. However, new cathode architectures (e.g., Prussian blue analogs) could push sodium-ion to 200 Wh/kg by 2027.