
What makes Cummins special?
Cummins engines stand out for their advanced combustion technology, industry-leading reliability, and innovative emission control systems. Their proprietary Celect™ electronic fuel system enables precise injection control up to 1,800 bar pressure, while non-EGR designs reduce component complexity. With B10 lifespans exceeding 2 million kilometers and smart features like EBP fuel optimization, they deliver unmatched durability and efficiency across commercial vehicles, construction equipment, and power generation systems.
What Is the Best Battery for a Diesel Pickup Truck?
What technological innovations define Cummins engines?
Cummins engines integrate four-valve-per-cylinder architecture, central injector placement, and articulated pistons for optimized combustion. The ISX12N natural gas variant demonstrates their commitment to alternative fuels, achieving near-zero emissions through stoichiometric combustion and three-way catalysts. Pro Tip: Always use factory-approved oil filters – their bypass valve settings protect against oil starvation during cold starts.
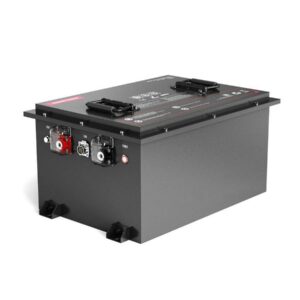
Cummins’ signature innovations begin with their Jacobs Engine Brake™, delivering 327hp of retarding power without fuel consumption. The steel-aluminum hybrid pistons uniquely combine thermal resistance (withstand 480°C crown temps) with vibration damping. Their XPI common-rail system’s 2,500-bar injection pressure ensures complete fuel atomization, reducing particulate matter by 63% compared to older models. For example, the X15 Efficiency Series achieves 55% brake thermal efficiency through improved turbo compounding. Transitionally, these technologies work synergistically – the Holset HE500VG turbo’s variable geometry maintains boost pressure down to 1,200 RPM, preventing lag during gear shifts.
How does Cummins achieve superior fuel economy?
The EBP SmartCoast® system and ADEPT™ predictive cruise control optimize fuel usage through terrain anticipation. Fleet data shows 6.2% MPG improvement in line-haul trucks using ADEPT’s pulse glide technology. Pro Tip: Maintain tire pressure within 5 PSI of spec – underinflation increases rolling resistance, negating engine efficiency gains.
Cummins’ fuel efficiency stems from three core strategies: combustion optimization, parasitic loss reduction, and driver coaching systems. The X12 engine’s 207g/kWh brake-specific fuel consumption results from 240-micron injection droplet sizing and 97% efficient turbochargers. Smart USFE algorithms analyze real-time load and grade data, adjusting torque curves to maintain optimal BSFC islands. Comparatively, their dual-stage fuel filtration prevents injector wear that typically degrades efficiency by 2% per 100,000 miles. Fleet operators report annual fuel savings exceeding $12,000 per truck when pairing Cummins engines with Eaton automated transmissions.
Feature | Cummins X15 | Competitor A |
---|---|---|
Peak Torque | 2,050 lb-ft @ 1,000 RPM | 1,950 lb-ft @ 1,200 RPM |
Service Intervals | 75,000 miles | 50,000 miles |
What makes Cummins engines durable in harsh conditions?
Cummins utilizes forged steel crankshafts and induction-hardened liners that withstand 25,000 PSI firing pressures. The QSK95 mining engine exemplifies this durability, operating 24/7 in Australian iron ore mines with 96% availability rates. Pro Tip: Conduct monthly coolant nitrate tests – electrolysis corrosion silently degrades cylinder walls.
Durability engineering starts with the Centinel™ Oil Management System that extends oil change intervals to 150,000 miles through real-time condition monitoring. Critical components like connecting rods undergo 10-million-cycle fatigue testing – three times industry standards. In cold climates, the Intake Air Temperature Modulation system prevents glaze formation on cylinder walls during extended idling. A real-world test in Canadian oil fields showed Cummins ISX15 engines achieving 1.2 million miles before overhaul versus 850,000 miles for competitors.
How does Cummins lead in emissions control?
Cummins’ Single Module™ aftertreatment combines SCR, DPF, and DOC in one unit, achieving 99% NOx conversion. Their 2025 X10 engine prototype demonstrates 0.02g/hp-hr NOx without urea dependency. Pro Tip: Use DEF with ISO 22241-1 certification – impurities in generic fluid crystallize and block injectors.
The emissions leadership stems from their closed-loop urea dosing and copper-zeolite SCR catalysts that maintain efficiency below 200°C. The X15N natural gas engine’s cooled EGR system enables lambda 1 combustion, reducing methane slip to 0.03g/hp-hr. Fleet data confirms 90% reduction in NOx compared to EPA 2010 standards. Transitionally, Cummins’ digital twin technology predicts DPF loading within 3% accuracy, enabling optimal regeneration scheduling.
Emission Component | Cummins Solution | Effectiveness |
---|---|---|
NOx Reduction | Advanced SCR with Ammonia Slip Catalyst | 99.5% |
Particulate Matter | Ceramic Wall Flow DPF | 99.9% |
Battery Expert Insight
FAQs
Why do Cummins engines last longer than competitors?
Precision-machined components with 5-micron bearing clearances reduce metal-to-metal contact. The PowerSpec® Plus calibration adds load-based derating protection, preventing catastrophic failures.
Can Cummins engines run on biodiesel?
All current models support B20 blends. The X15 HD specifically handles B100 through hardened fuel pumps and modified O-ring materials resistant to ester degradation.