
What destroys a lithium-ion battery?
Lithium-ion batteries degrade or fail due to overcharging, deep discharging, high temperatures, physical damage, and manufacturing defects. These stressors trigger irreversible chemical reactions (e.g., SEI growth, lithium plating) or thermal runaway, permanently reducing capacity or causing catastrophic failure. Proper BMS design and usage within 2.5V–4.2V/cell limits are critical for longevity.
Best Lithium Car Batteries for Cold Cranking Amps
How do high temperatures damage Li-ion batteries?
Prolonged exposure to >45°C accelerates electrolyte decomposition and SEI layer thickening, increasing internal resistance. At 60°C+, cathode breakdown releases oxygen, risking thermal runaway. Pro Tip: Store batteries at 20°C for minimal degradation—every 10°C rise above 30°C halves cycle life.
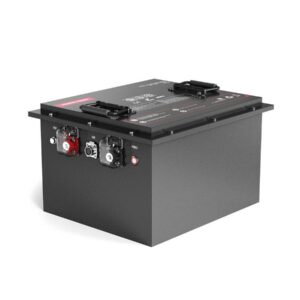
Heat triggers multiple failure modes. First, the solid-electrolyte interphase (SEI) on the anode thickens, consuming lithium ions and reducing capacity. Second, metallic lithium plating occurs during fast charging in hot conditions, creating dendritic shorts. For example, an e-scooter battery left in a 50°C trunk for 3 months may lose 40% capacity. Transitional phrase: Beyond temperature thresholds, chemical stability collapses. Why does this matter? Because even brief heat spikes during charging can cumulatively degrade cells. Always use thermal-regulated chargers in hot climates.
What happens during overcharging?
Voltage beyond 4.3V/cell forces excess lithium ions into the anode, causing metallic plating and electrolyte oxidation. This generates heat and gas, swelling cells or rupturing vents. Quality BMS systems prevent this by cutting off at 4.25V±0.05V.
Overcharging pushes cells beyond their electrochemical stability window. At 4.3V+, the cathode’s oxygen atoms bond with electrolyte solvents (EC/DMC), releasing CO2 and heat. The anode becomes lithium-saturated, plating metal instead of intercalating ions. Practically speaking, a single 4.5V overcharge can reduce cycle life by 70%. For instance, a DIY ebike pack using mismatched BMS/charger pairs might balloon within 10 cycles. Transitional phrase: Moreover, repeated micro-overcharges during trickle charging phases accumulate damage. Did you know? Some low-cost chargers fail to switch from CC to CV mode, risking voltage creep.
Overcharging Factor | Effect | Solution |
---|---|---|
Voltage >4.3V/cell | Anode lithium plating | Use precision BMS |
Continuous trickle charge | Electrolyte breakdown | Auto-cutoff chargers |
Can physical impact destroy Li-ion cells?
Yes—punctures, crushes, or bending breach separator membranes, causing internal shorts. This instantly dumps stored energy into heat (Joule heating), potentially igniting the flammable electrolyte.
Mechanical damage compromises the microporous polyolefin separator (typically 16–25µm thick). When anode and cathode materials contact, localized currents exceed 100A/cm², spiking temperatures to 500°C+ in milliseconds. A real-world example: A dropped power tool battery with cracked casing might appear functional until vibration shifts components, triggering sudden failure. Transitional phrase: In practical terms, even minor deformations matter. How? A 3mm dent from a wrench drop can stress internal jellyroll layers, creating latent short circuits. Always inspect batteries after impacts.
Why is deep discharging harmful?
Voltage below 2V/cell dissolves copper current collectors into the electrolyte, creating conductive dendrites. Upon recharge, these bridge electrodes, causing shorts and self-discharge. Cells discharged to 0V often become unstable paperweights.
At ultra-low voltages (<1.5V), the anode’s copper foil oxidizes into Cu²+ ions that migrate to the cathode. During subsequent charging, metallic copper precipitates, piercing the separator. For example, a forgotten drone battery left at 1.8V for 2 months might show 80% self-discharge/month post-recovery. Transitional phrase: Beyond voltage limits, recovery isn’t possible. Pro Tip: Set device cutoffs at 3.0V/cell—never rely on BMS low-voltage protection alone.
How do manufacturing defects cause failures?
Contaminants like metal particles or moisture during production create internal micro-shorts. Poorly welded tabs increase resistance, generating hot spots during high-current draws.
Defects often originate in electrode coating—uneven thickness (≥±2µm) causes lithium deposition irregularities. A case study: A 2022 EV recall traced to cathode aluminum foil fragments introduced during calendaring, which grew into dendrites after 200 cycles. Transitional phrase: Moreover, substandard purity in electrolytes (e.g., H2O >20ppm) accelerates HF acid formation. Why care? Because even ppm-level impurities catastrophically multiply over time.
Defect Type | Risk | Detection |
---|---|---|
Metal contaminants | Immediate internal short | X-ray scanning |
Moisture ingress | Gas generation/swelling | Karl Fischer titration |
Battery Expert Insight
FAQs
Can freezing temperatures damage Li-ion batteries?
Yes—charging below 0°C causes lithium metal plating. Store below -20°C is safe but only if cells are discharged to 40–50% SOC first.
Is it safe to mix old and new cells in a pack?
No—capacity mismatches force weaker cells into overdischarge. Always use same-age, same-batch cells with ≤2% voltage delta after grading.