What Battery Voltage Is Used In Trucks?
Truck batteries typically operate at 12V, 24V, or 48V, depending on vehicle size and application. Heavy-duty trucks often use 24V systems for reduced current draw and improved efficiency in starting/auxiliary power. Lithium-ion (NMC/LFP) and lead-acid are common chemistries, with lithium dominating newer models for higher energy density (150-200Wh/kg) and 3,000+ cycle life. Charging voltages range from 14.5V (12V systems) to 58V (48V architectures).
Why do heavy-duty trucks use 24V systems?
24V systems minimize current draw and voltage drop in long-haul trucks. By doubling the voltage, they halve the current needed for equivalent power (P=V×I), reducing wire thickness by 75% (I²R losses). Pro Tip: Never mix 12V and 24V accessories without DC-DC converters—reverse polarity risks frying ECUs.
Heavy-duty applications demand robust power delivery. A 24V battery system typically delivers 800-1500 cold cranking amps (CCA) for diesel engines, compared to 12V’s 400-700 CCA. This allows thinner 4 AWG cables instead of 0 AWG in 12V setups. For example, a Freightliner Cascadia uses twin 12V batteries wired in series to achieve 24V, supporting 2kW starter motors. However, what happens if one battery fails? Parallel cell degradation can cause unbalanced charging, stressing the alternator. Transitional phrase: Beyond voltage specs, cable routing matters—24V systems in trucks often employ star-topology grounding to prevent ground loops interfering with telematics.
12V vs 24V: Which is better for medium-duty trucks?
12V systems dominate light/medium trucks for compatibility with automotive accessories. 24V systems excel in heavy loads but require specialized components. Hybrid architectures (e.g., 12V starter + 24V accessories) are emerging.
Medium-duty trucks like Ford F-650 face a voltage crossroads. While 12V systems leverage cheaper, widely available parts (alternators: $200 vs 24V’s $450), they struggle with loads above 3kW. A 24V system running a refrigerated box can deliver 250A at 24V (6kW) through 2/0 cables, versus 12V needing 500A and bulky 4/0 wires. Pro Tip: For auxiliary loads over 2kW, 24V reduces fire risks from overheating connectors. Real-world example: Isuzu NPR trucks use 12V for starting but add 24V DC-DC converters for hydraulic lifts. But why not go all-24V? Transitional phrase: Practically speaking, retrofitting costs deter fleets—a full 24V upgrade averages $1,200 per truck for compatible radios, GPS, and lighting.
Factor | 12V | 24V |
---|---|---|
Wire Cost (20ft 4AWG) | $18 | $9 |
Alternator Cost | $220 | $410 |
Max Continuous Load | 1.8kW | 3.6kW |
How are lithium-ion batteries changing truck voltage standards?
Lithium-ion enables 48V architectures with 3-5x faster charging than lead-acid. Their flat discharge curves (13.2V-14.4V per 12V module) maintain stable voltage under load.
Truck manufacturers are adopting lithium to overcome lead-acid limitations. A 48V LiFePO4 battery can recharge to 80% in 45 minutes vs 4+ hours for AGM. Moreover, lithium’s 95% depth of discharge (vs 50% for lead-acid) effectively doubles usable capacity. For instance, Tesla Semi’s 48V system reportedly uses NMC cells with liquid cooling, delivering 1MW+ power. But what about cost? Transitional phrase: While lithium packs cost 2-3x upfront, their 10-year lifespan (vs 3-5 years for lead-acid) lowers TCO. Pro Tip: Always use a battery management system (BMS) with lithium truck batteries—cell balancing prevents thermal runaway during regenerative braking surges.
What voltage is used in electric truck propulsion systems?
Electric trucks use 400-800V packs for rapid charging and reduced current. Class 8 EVs like the Nikola Tre BEV employ 750V systems charging at 350kW, achieving 80% SOC in 90 minutes.
High-voltage traction batteries minimize resistive losses during energy transfer. A 600V system pushing 300kW only requires 500A, manageable via 150mm² cables. Comparatively, a 300V system would need 1000A and 250mm² wiring—adding 40kg+ per truck. Real-world example: Volvo FL Electric uses a 600V LFP pack modularly configured from 2.3kWh blocks. But why not higher than 800V? Transitional phrase: Beyond 1000V, insulation costs and arc-flash risks escalate. Pro Tip: When servicing HV systems, always use CAT IV 1000V-rated tools and follow lockout/tagout protocols—stray voltage above 50V DC can be lethal.
Voltage | Charging Rate | Typical Range |
---|---|---|
400V | 150kW | 200mi |
600V | 250kW | 300mi |
800V | 350kW | 450mi |
How does battery voltage impact truck accessory systems?
Higher voltage enables lower gauge wiring and efficient inverters for sleeper amenities. 24V systems power 3kW+ microwaves and HVAC without voltage sag.
Truck sleeper cabins increasingly demand hotel-like loads. A 24V system running a 2.5kW rooftop AC only needs 104A, allowing 6 AWG wiring. The same load on 12V would pull 208A, requiring expensive 2 AWG cables prone to voltage drop. Pro Tip: Use voltage-stabilized DC-DC converters for sensitive electronics like CPAP machines—direct 24V connections risk damaging 12V devices. For example, Peterbilt 579 Ultraloft offers 24V-powered 120V inverters supporting 5kW loads. But what if accessories need multiple voltages? Transitional phrase: Multi-voltage architectures are trending, with 48V for propulsion, 24V for HVAC, and 12V for legacy radios—all managed via smart power distribution modules.
Battery Expert Insight
FAQs
Yes, but ensure the BMS aligns with your alternator’s voltage profile. Lithium needs 14.4V±0.2V absorption—some OEM alternators only hit 13.8V, causing undercharging.
Do electric trucks use separate starter batteries?
No—EV traction batteries power all systems via DC-DC converters. A 12V auxiliary battery handles safety-critical loads during main pack shutdowns.
How long do truck batteries last?
Lead-acid lasts 3-5 years (1,000 cycles), lithium 8-12 years (3,000+ cycles). Extreme temperatures cut lifespan by 40% without thermal management.
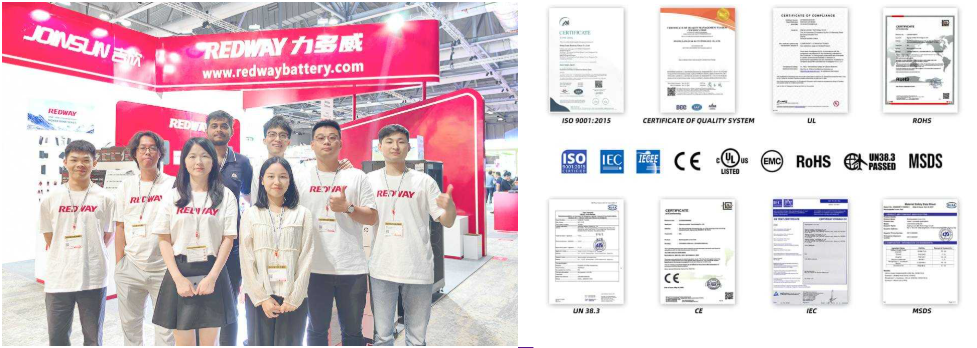