What Are Forklift Batteries?
Forklift batteries are heavy-duty energy storage units designed to power electric industrial vehicles. Typically using lead-acid or lithium-ion chemistries, they prioritize high current delivery for lifting and torque. Lead-acid variants dominate due to lower upfront costs, while lithium-ion offers faster charging and longer cycle life. Proper maintenance—like water topping for flooded lead-acid or BMS monitoring for lithium—is critical for maximizing their 5–10-year lifespan.
What types of forklift batteries are commonly used?
Forklifts primarily use flooded lead-acid (FLA), valve-regulated lead-acid (VRLA), or lithium-ion batteries. FLAs require regular watering but handle deep discharges, while lithium packs offer 3,000+ cycles with minimal maintenance. VRLA (AGM/gel) suits smaller fleets needing spill-proof operation.
Flooded lead-acid batteries operate at 24V–80V, with capacities from 250Ah to 1,200Ah. Their energy density is low (30–50 Wh/kg), but they’re cost-effective for multi-shift operations. Lithium-ion variants (LiFePO4 or NMC) deliver 80–150 Wh/kg, enabling 2–4-hour fast charging. Pro Tip: Always match battery chemistry to duty cycles—lithium excels in high-throughput warehouses. For example, a 48V 600Ah FLA battery weighs ~1,200 kg but provides 28.8 kWh, sufficient for 6–8 hours of medium-duty lifting.
Chemistry | Cycle Life | Charge Time |
---|---|---|
FLA | 1,500 | 8–10 hrs |
LiFePO4 | 3,500 | 2–3 hrs |
How do maintenance practices differ between chemistries?
Lead-acid demands weekly watering and terminal cleaning to prevent sulfation, while lithium-ion relies on BMS-controlled balancing. Equalization charges for FLA reverse stratification but aren’t needed for VRLA or lithium.
Flooded batteries require specific gravity checks (1.265–1.295) using hydrometers. Underwatering exposes plates, causing permanent capacity loss. Lithium’s sealed design eliminates fluid checks but needs quarterly cell voltage inspections. Pro Tip: Use deionized water for lead-acid—tap water minerals corrode plates. A warehouse using FLA reduced downtime 40% by automating watering schedules. Transitioning to lithium? Remember, their BMS can’t compensate for poor charger compatibility—always validate communication protocols.
What charging protocols optimize forklift battery life?
Lead-acid uses three-stage charging (bulk/absorption/float), while lithium-ion employs CC-CV with tighter voltage tolerances. Temperature-compensated charging prevents thermal stress in both types.
For FLA, absorption voltage is 2.45V/cell (e.g., 48V system charges to 58.8V). Lithium-ion (LiFePO4) stops at 3.65V/cell (58.4V for 16S). Pro Tip: Limit charge current to 0.2C for lead-acid and 0.5C for lithium to prevent overheating. Ever seen a swollen battery? That’s often from repeated overcharging.
Parameter | Lead-Acid | Lithium |
---|---|---|
Max Charge Temp | 45°C | 55°C |
End Voltage | 2.7V/cell | 3.65V/cell |
What factors reduce forklift battery lifespan?
Deep discharges below 20% SOC, excessive heat (>35°C), and partial charging degrade lead-acid. Lithium tolerates deeper cycles but suffers from high-current pulsing without proper cooling.
In lead-acid, sulfation starts below 50% SOC—a 48V battery shouldn’t drop under 46V under load. Lithium’s lifespan halves if kept at 100% SOC; storing at 50% prolongs longevity. A cold storage facility using lithium saw 15% longer lifespan versus lead-acid due to stable temperatures. But what about vibration? Forklift racks need shock-absorbent mounts—loose cells in lithium packs risk internal shorts.
How do costs compare between lead-acid and lithium forklift batteries?
Lithium costs 2–3x more upfront but saves 30–50% in long-term operational costs. ROI breakeven occurs around 3 years for high-utilization fleets.
A 36V 600Ah FLA costs ~$4,000 vs. $12,000 for lithium. However, lithium’s 3x cycle life and zero watering cut labor costs. Pro Tip: Calculate total cost per cycle—lithium often dips below $0.10/cycle versus FLA’s $0.15–$0.20. For example, a distribution center saved $28,000 annually by switching 10 forklifts to lithium, despite higher initial investment. But is lithium always better? For seasonal operations, lead-acid’s lower capital expense may still win.
Battery Expert Insight
FAQs
Replace lead-acid when capacity drops below 80% or voltage sags >15% under load. Lithium packs typically show gradual decline but monitor BMS error logs for cell imbalances.
Can I retrofit lithium into a lead-acid forklift?
Yes, but ensure the charger, cabling, and weight distribution match. Lithium is 30% lighter—counterweights may need adjustment for stability.
Are forklift batteries recyclable?
Lead-acid has 99% recycling rates. Lithium recycling is growing, with recovery rates up to 95% for cobalt and nickel through hydrometallurgical processes.
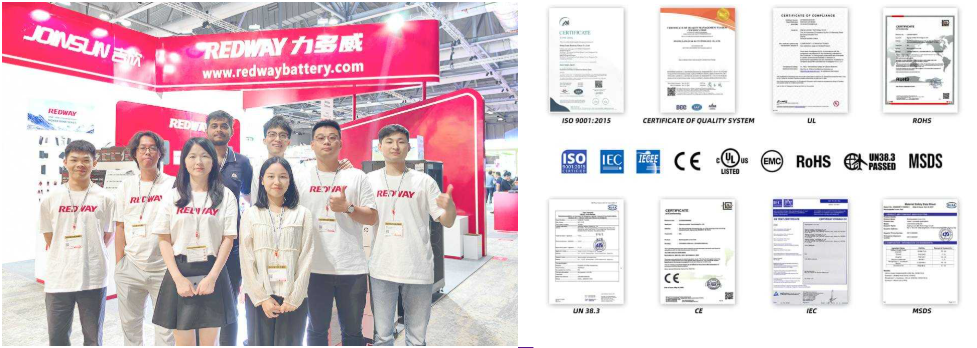