
How to tell if a diesel truck battery is bad?
Diagnosing a failing diesel truck battery involves checking physical symptoms, voltage performance, and load capacity. Key indicators include sluggish engine cranking (prolonged “clicking” sounds), visible corrosion/leaking, and voltage drops below 12.4V at rest or 9.6V during cranking. Use a multimeter for voltage checks and a load tester to measure cold cranking amps (CCA)—a 25% drop from rated CCA signals replacement. For example, a 800CCA battery reading ≤600CCA under load can’t reliably start diesel engines in cold weather.
How to Safely Dispose of and Recycle Car Batteries
What are the physical signs of a failing diesel truck battery?
Look for corroded terminals, bulging cases, or electrolyte leaks. White/green crust on terminals increases resistance, while case swelling indicates internal gas buildup from overcharging or sulfation.
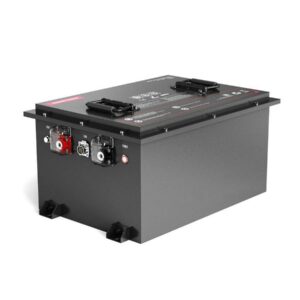
Diesel batteries endure higher vibration than passenger vehicles, so inspect mounting brackets for looseness—movement accelerates plate damage. Pro Tip: Clean terminals with baking soda/water (1:3 ratio) and apply anti-corrosion grease. A real-world example: A bulging Group 31 battery with 14.2V surface charge might still fail under load due to cracked internal plates from road vibrations.
How does voltage testing reveal battery health?
Resting voltage below 12.4V (12.6V–12.8V ideal) indicates partial discharge. Cranking voltage dipping under 9.6V confirms insufficient reserve capacity for diesel ignition demands.
Perform tests after 12+ hours of inactivity. For dual-battery systems, test each separately—weak cells often drag down paired units. Transitional example: A battery showing 12.1V at rest might recover after charging, but if it drops to 8V during cranking, internal sulfation has permanently reduced capacity. Why trust voltage alone? Because surface charge can mask deep-cycle damage—always combine with load testing.
Voltage (12V Battery) | State of Charge |
---|---|
12.8V–12.6V | 100%–75% |
12.5V–12.3V | 75%–50% |
<12.2V | <50% (Recharge/Replace) |
Why is CCA testing crucial for diesel batteries?
Diesel engines require 30%–50% higher CCA than gasoline equivalents due to compression ratios (16:1 vs 10:1). A 6.7L Power Stroke needs 850–950CCA versus 500CCA for a 5.0L gas V8.
Load testers apply ½ CCA rating for 15 seconds—voltage shouldn’t drop below 9.6V. For instance, testing an 800CCA battery at 400A load: 10.4V indicates health; 8.9V demands replacement. Transitional note: While CCA matters most in cold climates, heat accelerates electrolyte evaporation—inspect levels monthly in desert regions. Ever wonder why batteries fail in summer? Heat increases chemical activity but degrades plates faster.
Battery Expert Insight
FAQs
Can a diesel battery read 12.4V but still be bad?
Yes—surface charge may show normal voltage, but internal resistance from sulfation can collapse under load. Always perform CCA testing.
How often should diesel truck batteries be replaced?
Every 3–5 years, depending on climate and usage. Fleet vehicles in -20°C regions may need biannual CCA checks.