What Changes In Voltage Series Vs Parallel?
Series connections increase total voltage by summing individual cell voltages (e.g., six 12V batteries in series = 72V), while parallel connections maintain voltage but boost capacity (Ah) and current handling. Series setups suit high-power EVs like e-bikes, whereas parallel configurations prioritize runtime for devices like solar storage. Critical factors include cell matching and BMS compatibility to prevent imbalance. Pro Tip: Never mix old/new cells in parallel—unequal discharge rates cause overheating.
What defines voltage behavior in series vs parallel?
In series configurations, voltages add (24V + 24V = 48V), while parallel setups keep voltage constant but combine capacities (20Ah + 20Ah = 40Ah). This impacts energy delivery: series for high-speed motors, parallel for prolonged usage.
When batteries are wired in series, their voltages stack linearly. For instance, three 24V LiFePO4 cells in series create a 72V system—common in electric motorcycles needing high torque. However, it’s crucial to use identical cells; mismatched internal resistances cause voltage droop, reducing efficiency by 15–30%. Parallel connections, conversely, merge amp-hour ratings. Two 100Ah batteries in parallel deliver 200Ah at the same voltage, ideal for off-grid inverters requiring extended runtime. But what happens if one cell degrades faster? The healthier cell overcompensates, leading to accelerated wear. Pro Tip: Install fuses in parallel banks to isolate faulty cells. Real-world example: Tesla Powerwalls use parallel 21700 cells to scale capacity without exceeding home voltage limits (48V).
Configuration | Voltage | Capacity |
---|---|---|
Series | Summed | Same as single cell |
Parallel | Same | Summed |
How does series vs parallel affect device performance?
Series connections boost power for high-demand devices (e.g., EVs), while parallel setups extend runtime for low-power gadgets. Voltage dictates speed/torque; capacity determines how long devices operate.
High-voltage series systems unlock performance: A 72V e-scooter accelerates faster than a 48V model because voltage directly correlates with motor RPM. However, higher voltage demands thicker insulation and pricier components—think $200 vs. $120 controllers. Parallel systems shine in scenarios prioritizing endurance. A solar-powered CCTV camera with two 6V 200Ah batteries in parallel runs for 60+ hours instead of 30. But there’s a catch: parallel cells must share identical charge states. A 10% SOC difference between cells creates countercurrent flows, wasting 5–8% energy. Pro Tip: Use a balancer in parallel setups to synchronize voltages. For example, golf carts use 6x 8V batteries in series for 48V operation, delivering hill-climbing torque without sacrificing range.
Can you combine series and parallel configurations?
Yes, series-parallel hybrids balance voltage and capacity. For example, 4x 12V batteries in 2S2P yield 24V and doubled Ah. This approach customizes energy systems but demands rigorous cell matching.
Hybrid configurations solve niche challenges. Imagine building a 36V 40Ah pack from 12V 20Ah cells: two series pairs (24V) combined in parallel with another two pairs. Result? 36V isn’t achievable—this illustrates why planning is vital. Correctly, 3S2P (3 series, 2 parallel) of 12V cells creates 36V with 40Ah. These setups are common in electric boats, where 48V systems (4S) with parallel banks (2P) provide both thrust and 6-hour runtime. However, complexity escalates: a 3S2P pack has 6x the failure points of a single cell. Pro Tip: Label each cell’s position—mixing modules during replacement causes imbalance. Real-world example: Industrial UPS systems often use 4S3P lithium arrays for 48V and 300Ah, ensuring server backup during outages.
Design | Voltage | Capacity |
---|---|---|
4S1P | 48V | 100Ah |
2S2P | 24V | 200Ah |
What safety risks differ between series and parallel?
Series risks include overvoltage arcing (>100V DC is lethal), while parallel dangers involve thermal runaway from imbalanced currents. Each requires distinct protective measures—voltage monitors vs. current limiters.
In series strings, a single failed cell can induce cascading failures. If one 3.7V Li-ion cell in a 10S pack shorts, the remaining 9 cells force 37V through it, triggering combustion within seconds. Parallel systems face equalization hazards: a defective cell with 0.2Ω internal resistance (vs. 0.1Ω in others) will draw double current, overheating by 40°C+. Mitigation strategies diverge: series packs need HVIL (High Voltage Interlock Loop) circuits, while parallel banks require current-sharing ICs. Pro Tip: In parallel, use cells from the same production batch—manufacturing variances cause 5–15% resistance differences. Example: Nissan Leaf’s 192S1P module design avoids parallel connections, simplifying cell monitoring but limiting capacity scalability.
How to choose between series and parallel?
Prioritize series for voltage-sensitive devices (e.g., industrial motors) and parallel for capacity-critical apps (e.g., RV power). Hybridize only when necessary—complexity increases costs and failure risks.
Decision factors include load type and infrastructure. High-power devices like EV chargers (11kW+) require 400V+ series stacks to minimize current (I = P/V), cutting copper costs by 60%. Low-power gadgets like LED camping lights thrive on parallel AA cells—swap one dead battery without shutting down. But what if space constraints exist? Drones use 4S LiPo packs (14.8V) for compact high-speed motors, rejecting parallel options that’d add weight. Pro Tip: Calculate peak current—parallel’s lower voltage needs higher amps to meet power demands, risking connector meltdowns (e.g., 72V 10A vs. 12V 60A). Real-world example: Hospital UPS systems use 480V series strings (40x 12V) to power MRI machines efficiently, avoiding 12V parallel’s cabling nightmares.
Battery Expert Insight
FAQs
No—different chemistries have varying voltages (12.8V LiFePO4 vs. 12.6V lead-acid). Parallel connections force equal voltage, causing lithium cells to overdischarge lead-acid units, damaging both.
Does series wiring reduce battery life?
Yes, if cells aren’t matched. A weak cell in series drags the entire pack’s voltage down, forcing frequent deep discharges that degrade capacity 30% faster.
Why does parallel increase fire risk?
Faulty cells in parallel face higher stress currents—thermal runaway in one cell can cascade to others via shared busbars, unlike series where failures often isolate.
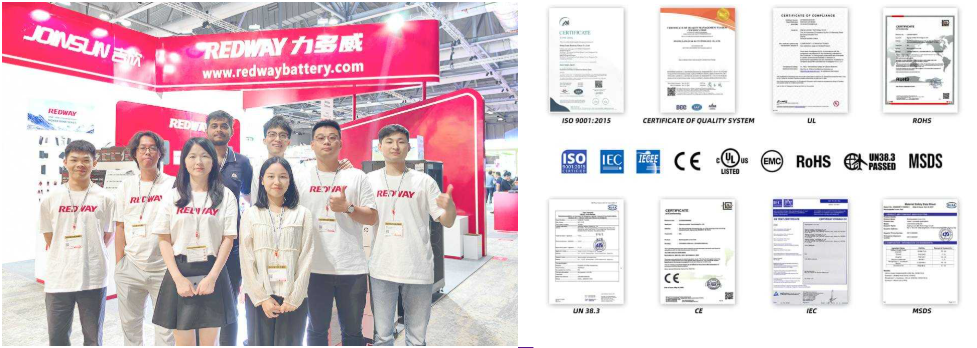